(Even if we often do not believe it!)
You often hear from problem solvers that while they solve sticky organizational issues, their bosses do not actually believe that their work activity contributes to the bottom line. The foregoing may often result because the relevant decision maker does not make a link between work activity and revenue generating ability in a business. However, we have to accept that all activity in a business, at some point will find its way to the income statement, either above or below the line, affecting the profit calculated.
Let us consider a simple problem: a production machine breaks down and after a few shifts becomes available for production again. Surely, if we orientate ourselves and think in Income Statement terms such a "Saleable Product, Raw Material, Labour Cost", then we are able to calculate the cost of the problem event/incident.
For example:
- > Lost profit - from product not produced
- > Fixed Cost - from product not produced (idle labour and infrastructure)
- > Additional Maintenance Cost to Material and Spare parts
- > Labour time to analyze and solve the problem.
The items mentioned above when tallied up for the duration of the problem event, will provide a reasonable estimate of what the problem incident costs the business. We can therefore conclude that the problem costs money, but how does the resolution of the problem reduce our costs in the long term?
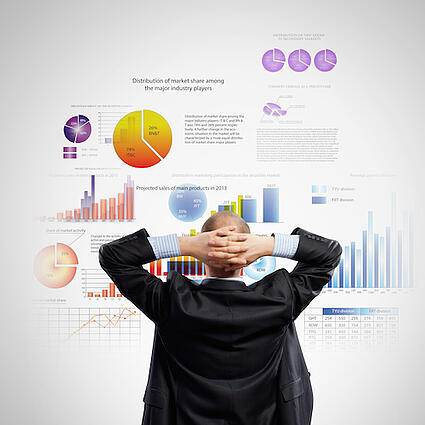
The true cost saving brought about by Root Cause Analysis is two fold:
- The longer it takes to solve a problem, the more expensive the problem becomes. Root Cause Analysts must therefore employ the right process to ensure conclusion and resolution in good time.
- The true savings associated with an incident is, however, an avoidance of future incidents. Root Cause Analysis should not stop when a problem is resolved; active analysis should be done to put plans in place to avoid the recurrence of the problem.
If we ensure that an incident does not reoccur, we will not have downtime, lost production or idle labour time. Add the items up from the current incident and you have the true cost reduction for the next incident occurring. Avoiding the future cost of a recurring incident is the true saving, because there is then no negative impact on the income statement.
In this sense, Cost Reduction = Root Cause Analysis.